Strengthening the battery value chain
Advancements in battery technologies are driving sustainability in global supply chains, enhancing power availability and reliability

Углекислый газ в двух словах
- The growing number of data centers, rise of renewable power generation and increased reliance on electricity in manufacturing is putting pressure on the existing electrical grid. Experts are investigating energy-augmentation technologies, such as microgrids and battery storage to address intermittency and capacity challenges during peak periods of demand.
- Battery technology has advanced rapidly over the past 50 years, spurred especially by the proliferation of portable electronic devices, laptop computers and more recently, the electric vehicle industry.
- While lithium is the primary element in most modern batteries, researchers are also exploring more affordable and reactive alternatives like sodium-ion batteries.
Lithium batteries
The battery manufacturing industry has experienced massive growth in recent decades, driven by the increasing importance of portability and flexibility in everyday life. The modern lithium-ion (Li-ion) battery started small, initially developed for use in consumer electronics in the 1990s, and it is now a staple in cellphones, laptops and more.
Tesla co-founder Martin Eberhard took a significant step forward by assembling multiple lithium batteries to power electric vehicles (EVs). He realized that the techniques used to produce laptop batteries could be adapted to manufacture these much larger batteries cost-effectively. As a result, Tesla and other EV manufacturers integrated it into the existing battery supply chain. The 2008 flagship Tesla Roadster was powered by 6,831 Li-ion laptop batteries, capable of a 400 km (250 mi) range and a top speed of more than 200 km/h (130 mph).
Beyond EVs, climate concerns are driving a transition toward sustainable power generation techniques, including wind, solar and geothermal. Battery storage is essential due to the intermittent generation capability of these energy sources. Modern lithium batteries are also increasingly used to continuously power microgrids, supplementing the traditional electrical grid. This is especially important for data centers and other applications with redundant power requirements.
Insights
The incorporation of multiple Li-ion batteries from laptops into one larger battery assembly made the first modern EVs practical.
The lithium battery value chain
Lithium passes through many steps and processes as it winds its way from the earth to wholesale and retail markets, including mining, refining, battery manufacturing and shipping. Therefore, the price of lithium batteries reflects all intermediary steps. Larger lithium batteries can be quite expensive. For example, a replacement Tesla Model S battery pack costs between USD $8,000 and $10,000.
The battery value chain consists of four main stages:
- Upstream: Miners extract lithium, cobalt, manganese, phosphates, nickel and graphite for use in Li-ion battery manufacturing.
- Midstream: Processors and refiners produce cathode and anode active components, and commodities traders buy and sell these active components to companies that assemble battery cells.
- Downstream: Battery manufacturers build cells into modules, which are then sold to wholesalers or consumer resellers.
- End-of-life: Battery recyclers break down spent batteries into individual components that are reused to produce new batteries, using a variety of methods.
Mining
Lithium is found in commercial quantities primarily in Australia, Argentina, Bolivia and Chile. In Australia, open pits of spodumene are used to process most of the lithium ore. The Greenbushes Mine in Western Australia is the world’s largest hard-rock lithium mine, producing approximately USD 5.6 billion worth of lithium spodumene annually.

In North and South America, lithium is concentrated from the salar brines found beneath ancient salt flats. Producers drill into these briny aquifers and then pump fluid into the drying beds, where most of it evaporates, leaving behind lithium salts. Other minerals like bromine can also be extracted from the concentrates in the drying bed.

Processing and refining
After raw materials are mined, they must be refined into usable formats. According to Bloomberg NEF , China, South Korea and Japan are the world’s top battery manufacturing countries. China currently dominates the global supply chain for Li-ion batteries, producing 80% of all Li-ion batteries, 70% of cathodes and 80% of anodes. Additionally, China processes and refines more than half of the world’s lithium, phosphate, cobalt and graphite.
The runners-up, South Korea and Japan, are responsible for significantly less battery production. South Korea produces 15% of the world’s cathode electrodes and 3% of its anode electrodes, while Japan accounts for 14% and 11%, respectively.
The lithium ore refining process adapts procedures from cement manufacturing, including grinding, calcination, milling and sulphation. Leaching and filtering are used to remove other minerals, such as alumina, manganese and calcium. This process continues until battery-grade lithium carbonate is obtained.
Manufacturing
Battery manufacturing requires assembling an entire battery cell and eventually an assembly of cells. Key components include cathode, anode and electrolyte. Li-ion cathodes are primarily made of lithium and anodes of carbon. Each cell includes a separator and case to hold the battery materials, which is filled with a conductive electrolyte.
The anode and cathode are made by creating a slurry that consists of active material, conductive agents and a binder. The slurry is then deposited onto a film or foil substrate. The foil is cut, trimmed and calendared, flattened between two pressurized rollers, to fit the battery and it is later dried. The solvent is recovered for reuse.
Once the anode and cathode are finished, a separator is installed between them. Then, the entire case is filled with electrolyte gel.
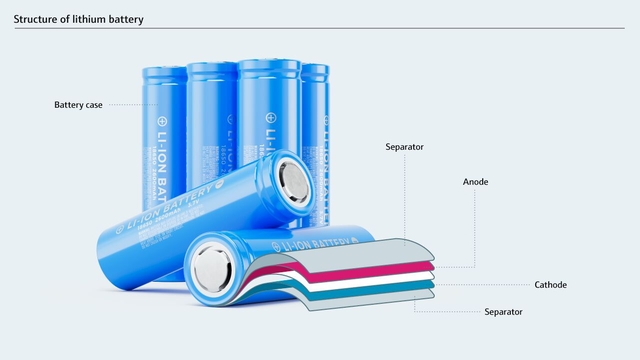
Supply chain challenges
Among typical supply chain challenges, the battery value chain possesses unique characteristics, requiring critical oversight to ensure safety and sustainability. First, supply chains must be carefully managed to ensure a consistent supply of brines, ores and other necessary raw materials. While substantial battery manufacturing is centered in China, raw materials come from all over the world, so any shipping interruptions can wreak havoc.
Furthermore, Li-ion battery manufacturing methods produce solid, liquid and gaseous waste. This creates the potential for adverse environmental impacts, especially in regions with lax environmental restrictions.
It is crucial to enforce strict standards for the manufacturing, disposal and recycling of Li-ion batteries due to their inherent risk of fire or explosion. Counterfeit batteries from questionable sources can exacerbate these hazards.
Recycling Li-ion batteries can also be difficult. Although considered hazardous waste, manufacturers can achieve significant energy savings by reusing these batteries, while eliminating the negative environmental repercussions of disposal.
Li-ion battery production costs are high due to the required quality of raw materials, the emphasis on quality control, complex manufacturing procedures and volume demand. For example, it takes 289 tons of ore, 750 tons of brine, or 28 tons of Li-ion batteries to produce one ton of pure, battery-grade lithium.
Insights
It takes 289 tons of ore, 750 tons of brine, or 28 tons of Li-ion batteries to produce one ton of battery-grade lithium.
Researchers are investigating the feasibility of sodium-ion batteries to address these challenges. Sodium is much more plentiful than lithium, easier to mine, and significantly less expensive. Additionally, it is less volatile and more stable.
Flow batteries, which store energy in a liquid electrolyte, are also under study for use in grid-scale energy storage. These types of batteries consist of two or more tanks to hold the electrolyte, whereby it is pumped through an electrochemical cell to produce electricity.
However, sodium-ion cells and flow batteries have lower energy density by volume and weight compared to Li-ion batteries. They are also less efficient, leading to less reliable end-use applications. Therefore, for the foreseeable future, Li-ion batteries remain the primary technology of choice.
Electrifying the future
Li-ion batteries have revolutionized portable power, enabling transformative technologies such as smartphones, power tools, EVs and microgrids. As the world shifts towards renewable energy and electric mobility, the demand for batteries will only grow. However, the complex and globally interconnected lithium battery value chain presents significant challenges.
Global sustainability requires ensuring ethical sourcing of raw materials, mitigating environmental impacts throughout the production process and tackling the battery recycling quandary. While electrochemical alternatives like sodium-ion batteries offer promise, Li-ion technology remains the dominant force in the battery sphere. Li-ion batteries are only a single component of global energy transition and carbon reductionefforts to achieve net-zero emissions by 2050.